Preface Reducing valve is through the opening and closing pieces of the throttle, the inlet pressure drop to a required outlet pressure, and the inlet pressure and flow changes, the use of its own medium energy outlet pressure to maintain the same basic valve. When the fluid flows through the pressure reducing valve, it will cause pressure loss, that is, energy loss. The energy lost in this part is the root cause of vibration and noise. It is inevitable that the pressure reducing valve will generate vibration and noise during operation. If the working pressure of the valve is too high, it will not only affect the health of the operator, but also threaten the safe operation of the entire equipment system. Such noise has been listed as one of the hazards. According to the relevant environmental regulations, if the noise of the pressure reducing valve is determined to exceed the allowable value of the standard, noise reduction measures must be taken. Therefore, the noise reduction valve in the piping system has aroused more and more attention. The author discusses how to determine the allowable noise of pressure reducing valve, analyzes the mechanism of noise when pressure reducing valve works, and puts forward effective noise reduction measures. Practice has proved that its noise reduction effect is obvious, satisfactory. 1, the allowable noise level of the valve In practice, the reasonable range of noise control valve has been a matter of concern. Reference to the relevant departments of environmental standards, labor safety standards and manufacturing standards of the valve, the valve allows the noise shown in Table 1 [1]. Table 1 Allowable noise level of pressure reducing valve Duration / h Allowable noise / dB 8 85 4 88 2 91 1 94 * The maximum allowable noise value should not exceed 115 dB In fact, in determining the noise allowable value of the pressure reducing valve, Considering the following various factors, the installation position of the pressure relief valve and its working environment; noise source power size; the operator's position and so on. For example, when the pressure reducing valve is in operation, if the operator is not in the vicinity of the valve, the allowable noise level of the pressure reducing valve can be appropriately relaxed at this time because the noise propagates twice as much as the propagation distance in the air Sound intensity will be attenuated by 6 dB. However, at a distance of 1 m from the noise source (ie, the pressure reducing valve), the maximum noise intensity should not exceed 85 dB, otherwise it is excessive. In taking measures to prevent noise, we should first determine the noise allowable value, and then noise prediction calculation. If the calculated value exceeds the allowable value, noise reduction measures must be taken. 2, the noise reduction valve noise source and the mechanism of noise reduction valve in the pressure-relief process, the consumption of fluid medium can be converted into heat, mechanical energy and the noise energy. To reduce noise, we must first convert the energy in the decompression process into as much heat as possible. The noise sources of the pressure reducing valve can be divided into three major categories as a whole: (1) parts of the pressure reducing valve generate noise due to mechanical vibration; (2) hydrodynamic noise; (3) aerodynamic noise. 2.1 Mechanical vibration noise The components of the valve when the fluid flow excitation will produce mechanical vibration, mechanical vibration can be divided into two forms: ①low-frequency vibration, the frequency of about 50 ~ 500 Hz, the sound pressure The level is about 90 dB. This vibration is caused by the jet and pulsation of the medium due to the flow velocity at the outlet of the valve being too fast, the piping arrangement unreasonable, and the rigidity of the valve movable part being insufficient. ② high-frequency vibration, the frequency of about 1000 ~ 8 000 Hz, the sound pressure level of 90 dB or more. This vibration causes a resonance when the natural frequency of the valve and the excitation frequency caused by the flow of the medium cause a certain resonance, which is generated by the pressure reducing valve within a certain pressure reduction range, and once the conditions are slightly changed, the noise change Great. This mechanical vibration noise has nothing to do with the medium flow speed, and such vibration noise can not be predicted in advance. Measures to reduce the mechanical vibration noise is to change the valve cavity shape and decompression area of ​​relief valve shape, reasonably design the clearance between bushing and valve stem, machining precision, natural frequency of valve and the rigidity of moving parts. Selection of materials. 2.2 Hydrodynamic noise Hydrodynamic noise is generated by the turbulence and eddy currents after the fluid passes through the relief port of the pressure relief valve. The process can be divided into two stages: ①turbulent noise, that is, The noise generated by the interaction of the fluid with the pressure reducing valve or the inner surface of the pipe is relatively low in frequency and noise level and generally does not constitute a noise problem. ② cavitation noise, that is, the decompression valve in the decompression process, when the fluid flow rate reaches a certain value, the fluid (liquid) began to vaporize, when the pressure in the liquid bubbles to a certain value, it will explode. Bubbles in the explosion, to produce local high pressure and shock waves, the impact pressure up to 196 MPa, but slightly away from the center of the explosion, the pressure decay sharply. This shock wave is a major contributor to the cavitation and noise of the pressure relief valve, with noise levels up to 100 dB or more. The pressure difference that produces cavitation can be expressed by Eq. (1) [2]. Δp initial = kc (p1-pv) (1) The pressure difference required for safe cavitation is given by equation (2): Δp critical = c2r (p1-pv) where p1 is the pressure at the valve inlet; pv For the liquid at the operating temperature of the saturated steam pressure; kc for the initial cavitation coefficient; cr for the critical flow coefficient. It can be seen from Eqs. (1) and (2) that when the actual pressure reduction value of the pressure reducing valve reaches the initial value of Δp, cavitation begins to occur in the liquid and the noise will increase sharply. Therefore, when designing a pressure reducing valve, it is necessary to control the pressure reducing value of the pressure reducing valve to be equal to or lower than the Δp threshold value, and preferably to be lower than or equal to Δp. In addition, pay attention to the flow direction of the fluid medium relative to the flap. 2.3 Aerodynamic noise When compressible fluid, such as steam, passes through the depressurization site in the relief valve, the noise generated by the conversion of the mechanical energy of the fluid into acoustic energy is called aerodynamic noise. This noise is a type of noise that is the most troublesome noise in the relief valve noise. The frequency of this noise is about 1 000 to 8 000 Hz, but it generally does not have a particularly steep peak frequency. The reason for this noise is divided into two situations, one is due to turbulence generated by the fluid, the second is due to the fluid to reach the critical flow rate caused by the shock wave. Aerodynamic noise can not be completely eliminated because it is inevitable that the pressure relief valve causes fluid turbulence when depressurized [3]. 3, reducing the pressure relief valve approach Valve in operation to consume a large amount of medium energy, some of these energy through friction, eddy current conversion to heat, the rest of the cause of mechanical vibration and collision, resulting in noise. In other words, these lost internal energy should be converted into heat as much as possible, so as to achieve the purpose of noise reduction. Figure 1 is a schematic diagram of the structure of a pneumatic valve, decompression hole is a slender light hole, the resistance according to equation (3) [4], that R = k1 × Q (3) where R Is the resistance value; Q is the fluid flow through the relief valve; k1 is the drag coefficient, k1 is related to the length of the hole, the form of the orifice and the roughness, etc. The longer the hole, the larger the roughness, the greater the drag coefficient. 1-ZMB-5 Pneumatic Film Actuator 2-ZPS-type handwheel mechanism From the above analysis we can see, in order to reduce noise, we must try to increase the value of R, so that decompression consume as much as possible Converted to heat rather than mechanical energy and sound energy. However, for large-caliber large-flow lift valve, the pressure relief hole length and roughness can not be too large. After years of exploration, I use threaded holes with greater resistance and can produce vortex principle, the decompression hole designed as a threaded hole in the form. On the one hand, by changing the flow direction of the fluid and reducing the medium jet velocity, the medium flows through the threaded hole in the valve body and then mixes in the sleeve to form a vortex to generate heat energy. On the other hand, The distance between the threaded holes is also an important factor affecting the noise reduction effect. The aperture of the threaded hole is too large, which not only results in unsatisfactory decompression but also has a poor noise reduction effect; the threaded hole is too small and easily blocked. The distance between the threaded holes is too large to cause a shock wave before it interferes with the jet beam; while the pitch of the threaded hole is too small, two adjacent jets will become a large jets and generate shock waves after mutual interference . Therefore, the hole diameter and spacing must be properly designed. The aperture of the screw hole is between M4 and M8, and the noise reduction effect produced when the pitch of the two screw holes is between 0.77 and 0.80 times is preferable. Now, this structure of the valve in several large domestic chemical companies to use the effect is very good. 4, Conclusion On the noise problem, it has been able to predict the calculation, and can take effective measures to prevent and reduce noise. After determining the allowed noise level, you can choose the most effective and economical method from a variety of measures. Practice shows that large-diameter large flow to enhance the sleeve decompression valve decompression such a special decompression hole, take the screw hole instead of the light hole approach, the process feasible, the valve can make the noise control noise-tolerant Within, the noise reduction effect is more ideal, which is an effective noise reduction measure.
Cardigan Sweater
Cardigan Sweater
Our cardigan sweater is colorful and comfortable to wear. It is definitely the most versatile, convenient and practical item to change in the cool season in the morning and evening. Cardigan sweaters can not only shade but also keep warm. Cardigan sweater is an essential fashion item in autumn. Its thin fabric allows you to wear lightly and keep warm.
If you are interested,please contact us.You can place order by sending pics or physical samples,and the custom designs or alternation on original is acceptable.
Yacheng Knitting Co., Ltd. can mass produce customized high-quality knitted garments, including sweaters, Custom Knit Sweaters, Knitted Pants, Knitted Skirt , Knitted Shoes, Knitted Scarves and Knitting Blanket. If you need to order knitted products, please contact us.
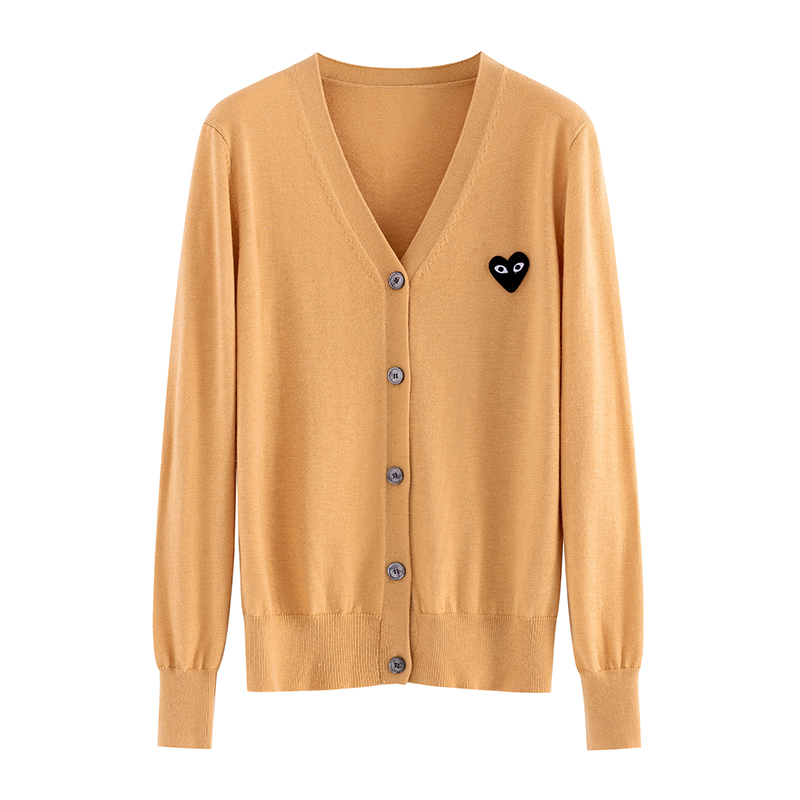
Cardigan Sweater,Cardigan For Women,Long Black Cardigan,Oem Women'S Sweater
DongGuan Yacheng Knitting Co., Ltd , https://www.oemknittingycs.com