Model: MS-50 (70mm)
1. Characteristics:
Power Supply: 220V± 5V 50Hz (60Hz)
Working Frequency: 20KHz
Output Frequency: 1500W
Working Speed: 0-18M/min
Effective Breadth: 0.1-100MM
Equipped Pattern Mould: (0.1-100)MMxØ 51MM
Materials Suitable: For Hot Fusibility, for example: Polyester, nylon, chemical and non-woven fabrics
2. Packing:
Packing Size: L (130cm)x W(60cm)x H(126cm)
Net weight: 125 Kgs
Gross weight: 140 Kgs
3. Functions:
1) The operations of side scraping and trimming
The side scrap in one side and side melting can be carried out at the same time. It makes the side smooth, no roughness and no coarse side.
2) Make holes
The holes with different patterns can be cut and the treatment of side melting can be carried out too.
3) Transfer printing
Two layers or multi-layers can be melted together. It is not necessary to use thread and needle. This process can replace sewing. Moreover the melted strength is excellent.
4) Cut Material
This machine can cut material for single piece or many pieces at one time. Moreover it can carry out the treatment of side melting. There is no coarse side.
5) Forming
Press the pattern wheel.
At one time the process of cutting, hole breaking and patter printing can be carried out.
4. Suitable material:
Composite material, thermoplastic film and plastics slice, such as chemical fibrous cloth, nylon cloth, knitting cloth, non spin cloth, gush glue cotton, PE paper, PE + aluminium, PE + cloth, and so on.
5. Application:
Lace clothing, skirt rim, sportswear, pajamas, gown, hair decorations, packaging satin, colored ribbon, tent, raincoat, tablecloth, chair cover, bedspread, pillowcase, quilt cover, curtain, handkerchief, coloured flag, disposable operating coat, non spin respirator, handicraft, decorations products.
6. Machine picture and samples
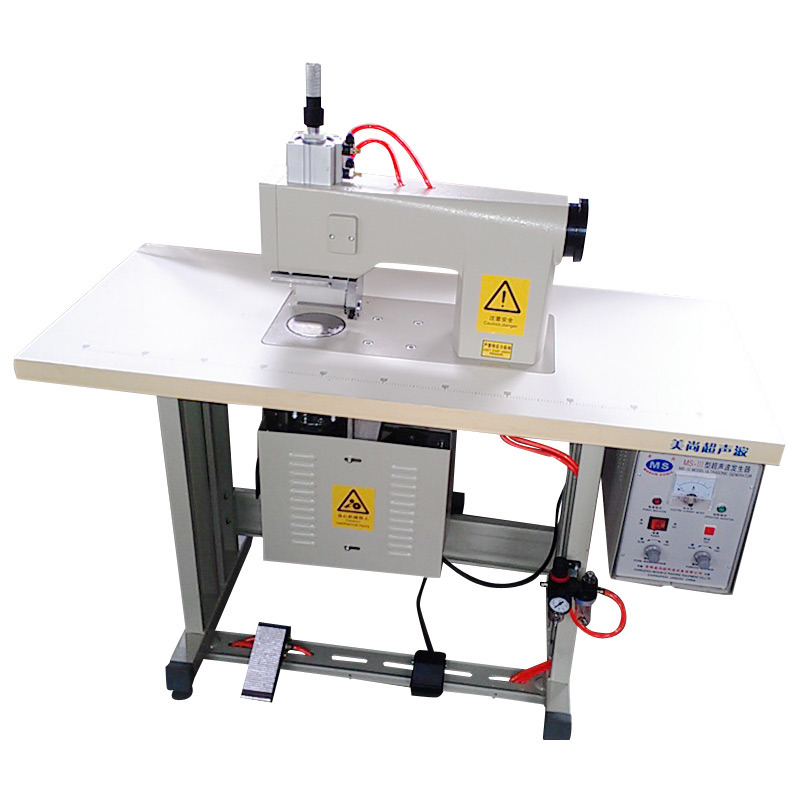
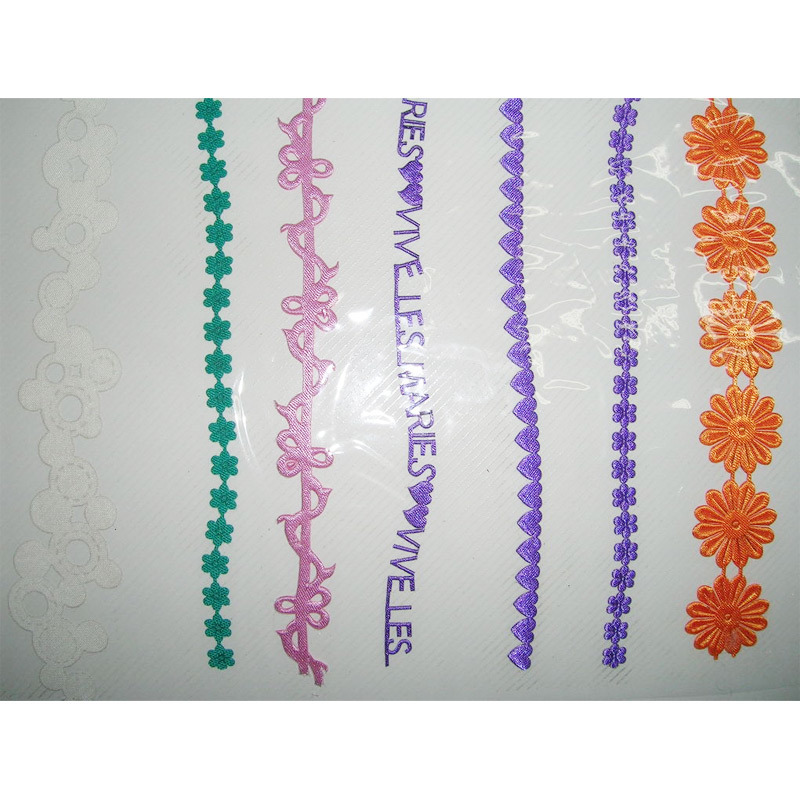
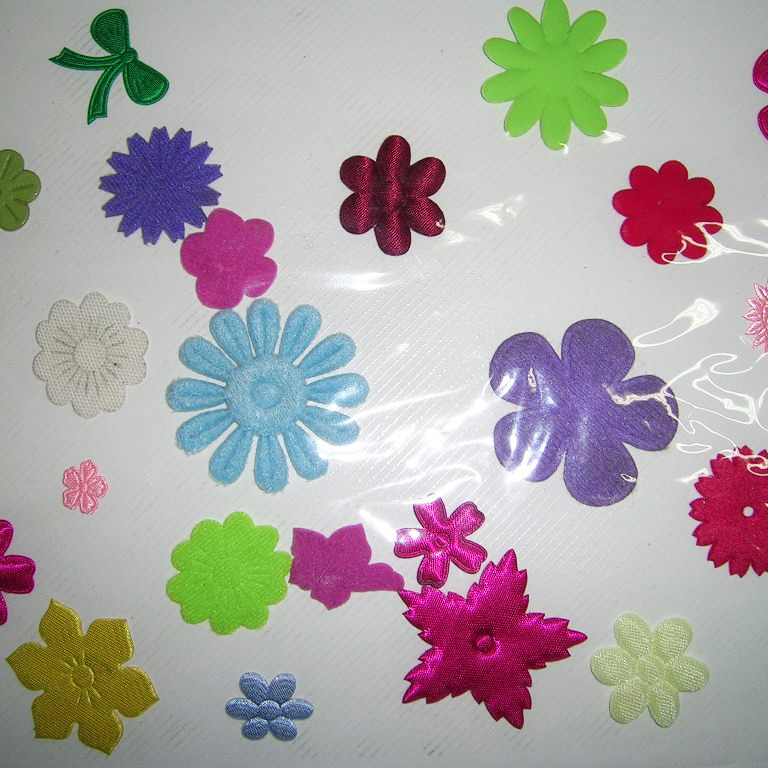
Power spinning is also called thinning spinning. Power spinning is a non-cutting processing method developed on the basis of ordinary spinning. When spinning, use the tail top to fix the blank on the mold. When the mold rotates, the rotating wheel makes a feeding motion, so that the blank continuously becomes thinner point by point and abuts against the mold to form a part of the required shape. Power spinning realizes the forming of the workpiece by changing the thickness and shape of the blank.
On airplanes, various nose covers, auxiliary fuel tanks, air intakes, gas cylinders, tie rods, slide rails, and actuators are all formed by spinning. In the engine, most of the propeller cap, casing, lip, intake cone, nozzle, nozzle, etc. are also formed by spinning. Such parts have complex structures, special raw materials, and large product sizes. The use of spinning forming can improve the integrity of structural components, reduce welds and component deformation, and reduce the workload of manual calibration. More importantly, due to the increased strength of the material after spinning, the design wall thickness of the parts can be reduced, thereby reducing the weight of the whole machine and improving the reliability of the whole machine.
Heavy Duty Spinning,Cnc Metal Spinning,Metal Spinning Machine,Metal Spinning Lathe
Jiangsu Hoston Machine Tools Co., Ltd. , https://www.haostonmachinetools.com